3D Printed Functional Organic and Inorganic Materials and Devices
Nowadays, 3D printing or additive manufacturing has been applied to a variety range of materials, from polymers, metals to ceramics. Within the 3D Matter Made To Order (3DMM2O) cluster of excellence, our focus is to characterize and understand the local structure and functional properties of 3D printed organic and inorganic materials and devices. By employing the state-of-the-art analytical electron microscopy techniques in combination with in-situ and ex-situ stimuli, we aim to provide insights into these 3D printed metamaterials in atomic, nano and micro scales, facilitating the tailoring of novel materials and devices in a bottom-up manner.
In Situ Pyrolysis of 3D Printed Building Blocks of Functional Nanoscale Metamaterials
Contact: Qing Sun, Prof. Dr. Yolita Eggeler
3D nanolattice metamaterials have exceptional lightweight and unprecedented mechanical properties, which are derived from the geometry of their internal periodic structures rather than the properties of the constituent materials [1]. One promising way to fabricate 3D nanolattices is direct laser printing (DLW) of polymeric precursors based on two-photon polymerization (TPP) combining with a subsequent pyrolysis step [2]. The latter will introduce a great mass loss and volumetric shrinkage by outgassing when temperature goes up to around 400-600 °C for most polymers. However, a comprehensive and predictable shrinkage behavior is remaining to be studied.
In this work, we aim to systematically investigate the shrinkage dynamics of 3D printed microstruts by in situ environmental scanning electron microscopy (ESEM) heating. These 3D printed microstruts are used as building blocks for functional nanolattice metamaterials. As a novel approach for sample preparation, we directly print IP-Dip photoresist on Micro-electromechanical Systems (MEMS) based heating chip. The schematic is presented in Figure 1 [3].
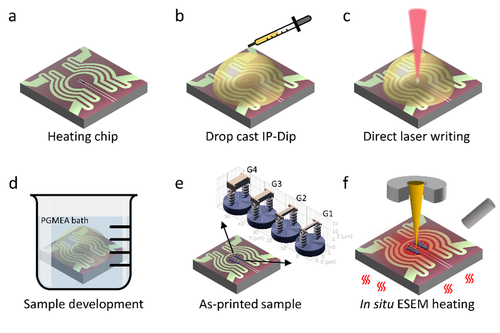
the micro-electro-mechanical systems (MEMS) chip by two-photon DLW
for in situ ESEM heating.
To correlate the effects of temperatures, atmospheric pressures as well as surface-to-volume ratios on isothermal shrinkage, we performed six in situ ESEM experiments at three temperature settings: 450, 500 and 550 °C, in two pressure regimes: high vacuum (HV) of 10−5 mbar and in a reduced nitrogen atmosphere of 3 mbar (LV), and on a series of microsturts with four different sizes: G1-G4. For the first time, the structural evolution of 3D printed structures is tracked continuously until a quasi-stationary state is reached (see Movie 1 [3]). The movie is generated by a stack of SEM images that are recorded continuously during the isothermal processes. Besides thermal dependence, i.e., the higher the temperature, the faster and greater the contraction, we observed the influence of environmental pressures. By tracking the strut length change, Figure 2a illustrates how the increased partial pressure (nitrogen atmosphere) altered the shrinkage behaviors.

of IP-Dip microstruts in a high vacuum of 10−5 mbar at 500 °C.

in high vacuum (HV) and low vacuum (LV) conditions. a) Pyrolysis kinetics
of in situ heating experiments at 500 °C for two different atmospheric regimes:
normalized length (projected) of each microstrut with respect to heating time
in one hour. b) The effective activation energies for the microstruts with
different cross-sections (G1– G4) in high and low vacuum conditions.
Furthermore, we investigate the cross-sections of these heated microstruts in an analytical transmission electron microscope (TEM) to get more insights into the diffusion/degassing process during pyrolysis. These cross-sections are prepared by focused ion beam (FIB) cutting. Scanning transmission electron microscopy (STEM) combined with electron energy loss spectroscopy (EELS) is a powerful characterization method that allows to measure not only atomic composition, but also chemical bonding with high spatial resolution. The carbon and oxygen mappings in Figure 3 confirm an additional oxygen enriched contour (oxygen outer ring) accumulated only around the surface of the samples that are pyrolyzed in nitrogen atmosphere (LV).

heating conditions by STEM-EELS. Left panel: Bright field (BF-) STEM images
of the cross-sections of microstrut G4 prepared by FIB cutting. Right panels:
Two columns of spectrum images showing the carbon (left) and oxygen (right)
distribution in the micorstruts cross-sections.
Besides SEM and TEM investigations, we performed model-free master curve approach [4] to calculate the effective activation energy Eaeff from these pyrolysis-induced shrinkage curves. Its results (Figure 2b) reveal that Eaeff is approximately four times larger under vacuum conditions than in a nitrogen atmosphere (2.6 eV vs. 0.5–0.9 eV, respectively). Additionally, this in situ experimental pyrolysis design can be extended to investigations of various other polymer precursors and additive manufacturing methods.
[1] Bauer, J., et al. (2017). "Nanolattices: An Emerging Class of Mechanical Metamaterials." Advanced Materials 29(40): 1701850.
[2] Eggeler, Y. M., et al. (2023). "A Review on 3D Architected Pyrolytic Carbon Produced by Additive Micro/Nanomanufacturing." Advanced Functional Material: 2302068.
[3] Sun, Q., et al. (2023). "In Situ Pyrolysis of 3D Printed Building Blocks for Functional Nanoscale Metamaterials." Advanced Functional Materials: 2302358.
[4] Niekiel, F., et al. (2015). "The process of solid-state dewetting of Au thin films studied by in situ scanning transmission electron microscopy." Acta Materialia 90: 118-132.